
FREQUENTLY ASKED QUESTIONS
HINT: PRESS CONTROL + F KEYs ON A PC (OR COMMAND + F KEYs ON MAC) TO SEARCH ON THIS PAGE
Q. CAN YOU SANDBLAST OR POWDER COAT CAR PANELS / BODIES?
A. Our abrasive blasting facilities are targeted towards industrial applications with large grit delivery at high pressure and are not suited to blasting of car panels. Excessive heat and pressure from the blast equipment can result in warping and deformation of thin sheet metal ultimately damaging the metal surface. as such, we do not recommend our blast equipment for abrasive blasting of thin sheetmetal items such as car bodies and panels.
Q. WHAT SIZE PRODUCTS CAN YOU PROCESS?
A. Our facilities can handle a wide variety of part shapes and sizes. Depending on the services your product requires i.e. abrasive blasting, pre-treatment, priming and/or powder coating, the dimensions and capacities of our processes are outlined on our Capacity page located here.
Q. CAN YOU RECOAT OVER EXISTING POWDER COAT?
A. Re-coating of powder coated materials can be completed, however due to a number of factors the results from recoating of products are less certain than finishing of new and sandblasted materials. In general, powder coated goods that are clean, free from contaminants, rust / corrosion and checking or flaking of the finish have a reasonable chance of being recoated successfully. For re-coat jobs we implement a number of product specific practices to increase the likelihood of successful re-coating results, however due to the potential for defects and/or contamination of the underlying coating / surface we cannot provide any assurances that the performance or life of the coating will be suitable in any application in the short or long term. Subsequently re-coating is not recommended if customers require an 'As New' finish but may be suitable for customers looking to bring fresh life to an old coating at a reduced cost.
Q. CAN YOU POWDER COAT OVER ANODISED ALUMINIUM?
A. Anodised aluminium is not recommended for powder coating as our standard pre-treatment process (chromate conversion pre-treatment) cannot contact and treat the raw aluminium substrate due to the presence of the anodised layer. In general, powder coating plants do not have the facilities to adequately strip the anodised layer from the metal due to the low demand and high cost for stripping relative to supply of mill finish (raw aluminium) materials for powder coating. As we cannot control the surface preparation for anodised aluminium materials, we do advise customers to provide mill finish materials for powder coating where possible. In circumstances where customers request we complete powder coating over anodised aluminium against our recommendation, we cannot provide any assurances that the performance or life of the coating will be suitable in any application in the short or long term.
Q. WHAT CAN BE POWDER COATED?
A. Powder coating is designed for the coating of conductive metal surfaces, principally items made from aluminium, black steel and zinc coated (galvanised) steel. In general, any metal items that can withstand the baking temperatures of approximately 220 Deg Celsius can be powder coated. Powder coated items are seen by most people everyday without even realising it, typical powder coated items include whitegoods such as washing machines and dryers, bicycle frames, 4WD accessories such as bulbars and roof racks etc, metal furniture, fencing, security screens, blinds and awnings and more.
Q. CAN YOU POWDER COAT HOT DIPPED GALVANISED (HDG) STEEL MATERIALS?
A. Hot dipped galvanised materials are suitable for powder coating provided they have been requested as air-quenched from the galvaniser. Due to the reduced effectiveness of our standard pre-treatment process on water-quenched HDG materials, we do not provide any assurances whatsoever that the performance or life of the coating will be suitable in any application in the short or long term for materials provided in this form. Powder coating of hot dipped galvanised materials may result in surface irregularities in the finish due to the underlying HDG surface and release of entrained gases within the galvanising layer. Our standard service does not include any sanding, filing, or preparation of the galvanised surface. Customers who are concerned with the quality and longevity of the surface finish should elect for optional heat treatment of the material prior to processing, select a degassing powder from the Interpon Excel™ range and/or elect for optional surface preparation treatment to reduce the frequency of irregularities in the galvanised surface.
Q. WHAT DO I NEED TO DO TO GET MY ITEMS READY FOR POWDER COATING?
A. There are a number of things to consider when preparing your item for powder coating, some of which depend on the process required to complete your item.
Abrasive Blasting:
Thin sheetmetal can be deformed by the pressure and heat of the blast gun and is not recommended for processing
Severe corrosion of the item and/or fillers within the existing coating may result in holes and/or depressions in the product finish
Any stickers/decals, rubber, plastic, electrical, bearings, seals and/or silicon should be removed from the product prior to processing as these may be damaged by abrasive blasting
Products should be thoroughly degreased to be free from oil or grease for further processing
Chemical Pre-treatment:
All seal welded compartments need a minim of 2 x 5mm did holes to allow free entry and drainage of pre-treatment chemicals
Products should be free of stickers, markings with permanent or paint markers or adhesives as these will not be removed by the pre-treatment chemicals
Powder Coating & Priming:
Products should be free from low melting point metals e.g. solder as these will melt and/or lose strength from exposure to elevated oven temperatures
Products should have holes or hanging points available within their design in order to suspend the item in a fan forced oven
Product should be free of contaminates such as oil, grease, adhesive tape, stickers, rubber, plastic, wax, silicone etc as these can result in defects in the finished product
Q. CAN YOU POWDER COAT DURAGAL® MATERIALS?
A. Duragal® and similar galvanised steel sections are typically coated in a clear polymer coating to protect the galvanised coating from exposure to the environment during handling and manufacture. Due to the presence of the polymer layer (without removal), application of a powder coating to the product in effect will be applied on top of the clear polymer layer rather than directly to the metal surface; potentially impacting the adhesion and associated durability of the applied powder coating. The suitability of these galvanised products for powder coating varies by manufacturer and specification and therefore we recommend customers supplying these materials confirm with their metal supplier regarding suitability of such materials for powder coating. Alternatively, if suitability cannot be confirmed we recommend removal of the polymer layer through a quick whip blast and priming prior to powder coated to provide the most durable coating for these products. In circumstances where customers request we complete powder coating over Duragal® or similar materials without confirmation of suitability for powder coating and against our recommendation of whip blast preparation, we do not provide any assurances that the performance or life of the coating will be suitable in any application in the short or long term.
Note: Duragal® is a registered trademark of Austube Mills Pty Ltd and is used to provide example of zinc coatings typically supplied with a clear polymer layer over the zinc coating.
Q. CAN WATER DAMAGED ALUMINIUM BE POWDER COATED?
A. Aluminium materials that have been water damaged are unable to be effectively treated through our standard pre-treatment process without prior physical removal of any water damaged areas using abrasive or mechanical means (e.g. buff / grinding wheel, abrasive blasting etc). We can completed removal of water damaged areas from external areas prior to processing for additional cost, if you have water damaged aluminium materials that you wish to powder coat please let us know and we can discuss options with you on a case by case basis.
Q. CAN YOU POWDER COAT STAINLESS STEEL?
A. Stainless steel materials are suitable to be powder coated. As standard chemical pre-treatment processes are not designed for stainless steel, we do recommend whip blasting of stainless steel surfaces (especially polished stainless steel) prior to powder coating to provide better mechanical adhesion of the coating to the stainless steel surface for a long lasting, durable finish.
Q. DO YOU ANODISE ALUMINIUM?
A. E-static Powder Coating can complete powder coating finishes that are similar in appearance to a number of anodised finishes however we do not offer anodising services at this time. If you would like to see our powder coated finishes that replicate anodised aluminium finishes, please drop in and look at our colour sample board in store.
Q. DO YOU DO CERAMIC COATINGS?
A. E-static Powder Coating do not offer ceramic coating services at this time.
Q. WHAT TEMPERATURE IS POWDER COATING ABLE TO WITHSTAND?
A. Although powder coating is cured at elevated temperatures, it is not deigned as a coating suitable to exposure to high temperature or elevated temperatures for an extended period of time. Recommended maximum temperatures vary depending on the powder and manufacturer however they are typically designed for environmental temperatures conditions of less than 70 degrees celsius. Exposure to temperatures above this may result in degradation of the finish over time and therefore is not recommended.
Q. CAN YOU POWDER COAT OVER PAINT?
A. In most cases we are unable to powder coat over paint as it is typically not designed to handle exposure to elevated cure temperatures within the powder coating cure oven. Furthermore, there are are only limited paint finishes that are designed for being coated with powder coat and are generally limited to metal primer paints. Therefore as a general rule, powder coating cannot be applied over paint and therefore we generally remove any paint from metal surfaces using our abrasive blasting facilities prior to powder coating.
Q. CAN YOU MIX TO MATCH OR MAKE A CUSTOM COLOUR?
A. Powder coating finishes are sprayed on in a solid powder form and therefore unlike liquid paints are unable to be mixed to colour by finishers. However, a wide variety of standard colours are available from leading powder manufacturers such as Interpon and Dulux Powder Coatings. Furthermore, if colours from the standard range are not able to meet your requirements, custom colour manufacturing is available on request.
Q. DO YOU DO CHROME PLATING?
A. E-static Powder Coating can complete powder coating finishes that are similar in appearance to a chrome plated finish however we do not offer chrome plating services services at this time. If you would like to see our powder coated finishes that replicate chrome plated finishes, please drop in and look at our colour sample board in store.
Q. HOW DURABLE IS POWDER COATING?
A. Powder coated finishes are a baked on plastic finish that is typically harder and thicker than liquid paint alternatives. Subsequently the finish is generally more resistant to chips, scratches and wear than liquid paint finishes and is subsequently considered more durable in many product applications. Notwithstanding the high durability of powder coating, care should always be taken to protect the coating during handling and use as with sufficient force or exposure to hash chemicals or conditions the coating can still be damaged.
Q. HOW DO YOU GET POWDER COATING TO STICK TO MY PRODUCT?
A. Powder coating is applied through an electro-static spray process whereby the solid powder materials are charged up to a high voltage through the specialised spray equipment. The part being coated is connected to ground / earth and subsequently the charged particles are attracted to and stick to the part using forces created from the static charge of the powder particles. The coated part is then heated in an oven at elevated temperature to melt and cure the coating into a consistent coating layer on the product.
Q. WHAT IS POWDER COATING?
A. Powder coating is a decorative coating traditionally applied to metal products as a superior substitute to wet paint systems for many applications. The term powder coating is derived from the solid powder-like physical state of the raw coating materials prior to application (as opposed to liquid based coating alternatives such as paint). The powder material (most typically a thermosetting plastic) is electrostatically applied to materials through specialised application equipment and cured in an oven at elevated temperature to melt and chemically transform the applied powder layer to a consistent hard, durable and decorative protective coating of the product surface.
The concept of applying an organic polymer in powder form dates back to the late 1940s and early 1950s when powders were flame-sprayed on metallic substrates. In 1953, Dr. Erwin Gemmer developed the fluidized bed application method which was virtually the only method of powder coating application through until the mid sixties. Electrostatically applied thermosetting powder coating in its current form was developed in Europe in 1962 by Pieter de Lange while working for Teodur (now part of DuPont Powder Coatings) in response to a need for more environmental friendly coating processes than spray paints.
Q. WHAT COLOUR CHOICES DO YOU HAVE AVAILABLE?
A. There are a wide variety of standard colours available from leading powder manufacturers such as Interpon and Dulux Powder Coatings. Specialty colours, finishes and other powder manufacturers products including PPG and Jotun are also available upon request. Furthermore, if colours from the standard range are not able to meet your requirements, custom colour manufacturing is available on request. Check out our Colours page to click through to colour charts from some of our leading powder suppliers.
Q. WHY DO YOU USE AN OVEN IN POWDER COATING?
A. Powder coating typically involves the process of applying a layer of thermosetting plastic in powder form to a part using an electrostatic spray process. In order to transform the applied plastic powder into a hard consistent finish, products are heated in specially designed industrial ovens whereby the applied powder melts to form a consistent layer and undergoes a chemical reaction to provide a hard coating once the temperature returns to room temperature.
Q. HOW LONG WILL IT TAKE TO GET my item POWDER COATed?
A. The length of time required depends on the steps required for powder coating your item and the service priority you require. We offer a fast and consistent turnaround as part of our standard service. For customers that require goods to completed in a more timely manner we also offer an Express service priority to get your items back to you as fast as possible (additional charges apply).
Standard Priority:
For new aluminium and galvanised steel items that require chemical pre-treatment and powder coating, under our standard service we target to complete your goods within 5 working days from when you drop them off with us.
For items that require sandblasting prior to powder coating, we target to complete your goods within 8 working days from when you drop them off with us.
Express Priority:
For new aluminium and galvanised steel items that require chemical pre-treatment and powder coating, under our standard service we target to complete your goods within 2 working days from when you drop them off with us.
For items that require sandblasting prior to powder coating, we target to complete your goods within 4 working days from when you drop them off with us.
Please note that these times can be subject to prevailing and seasonal demand for our services and are provided as a general guide to customers, we will advise at time of receipt of your goods if we are unlikely to meet these standard turnaround times.
Q. I ONLY HAVE A SMALL ITEM, WHAT ARE YOU MINIMUM ORDER SIZES?
A. We have the ability to powder coat items both large and small, however due to the effort required to manage each job and the time taken to setup, spray and clean out spray equipment after your selected finish has been applied, minimum costs do apply on a per colour basis. However the minimum job cost is very reasonable and in some cases enables you to bring multiple small items to be processed in the same colour at the same time for no extra cost. Contact us today to discuss your small items and we will be happy to provide a cost to complete.
Q. DO I NEED TO MAKE A BOOKING TO GET MY ITEM POWDER COATED?
A. No bookings are required to get your items powder coated, simply drop by with your goods and we can get to work on powder coating them for you as soon as possible.
NEED SOMEthing powder coated?
Contact Us
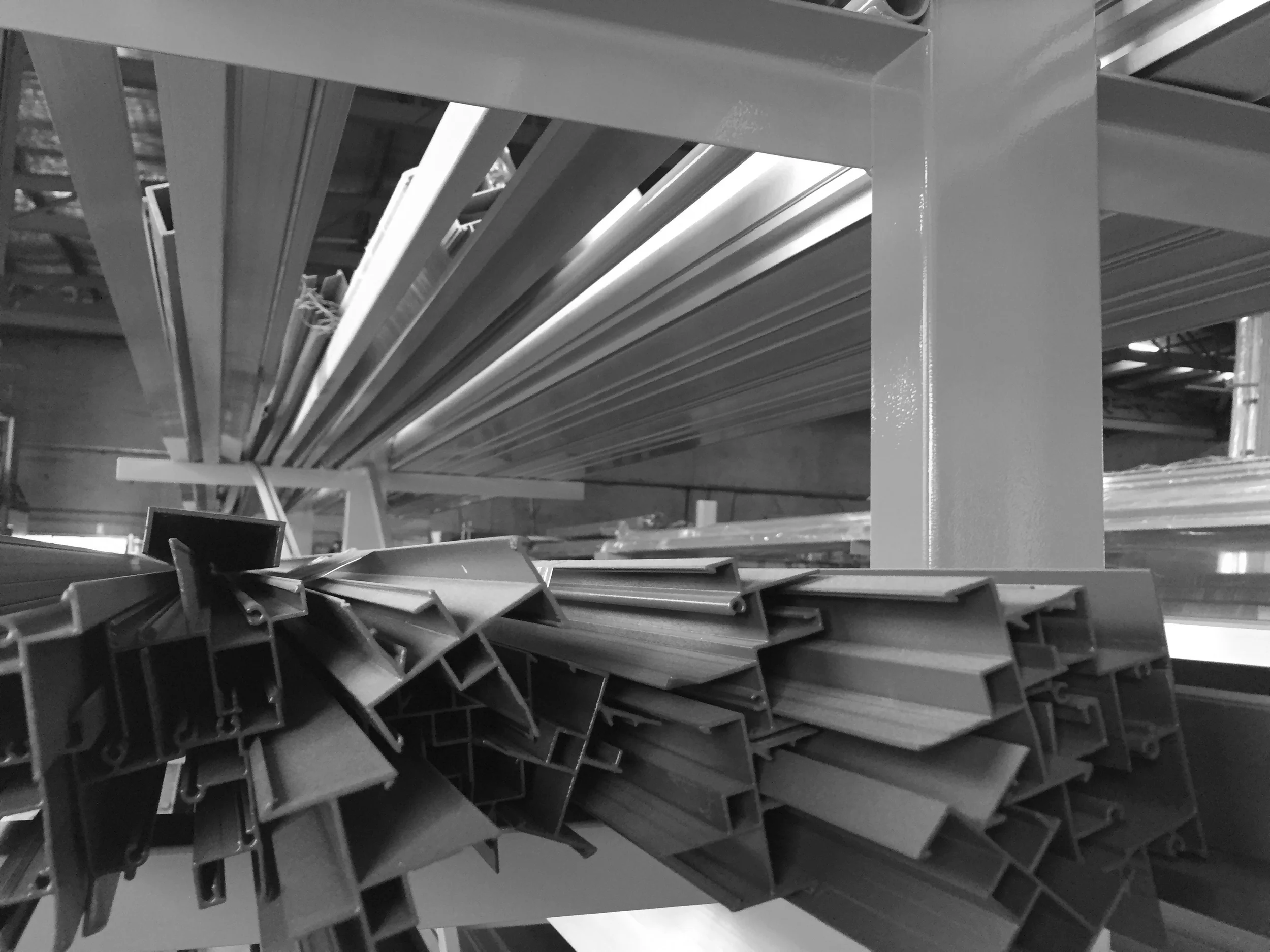